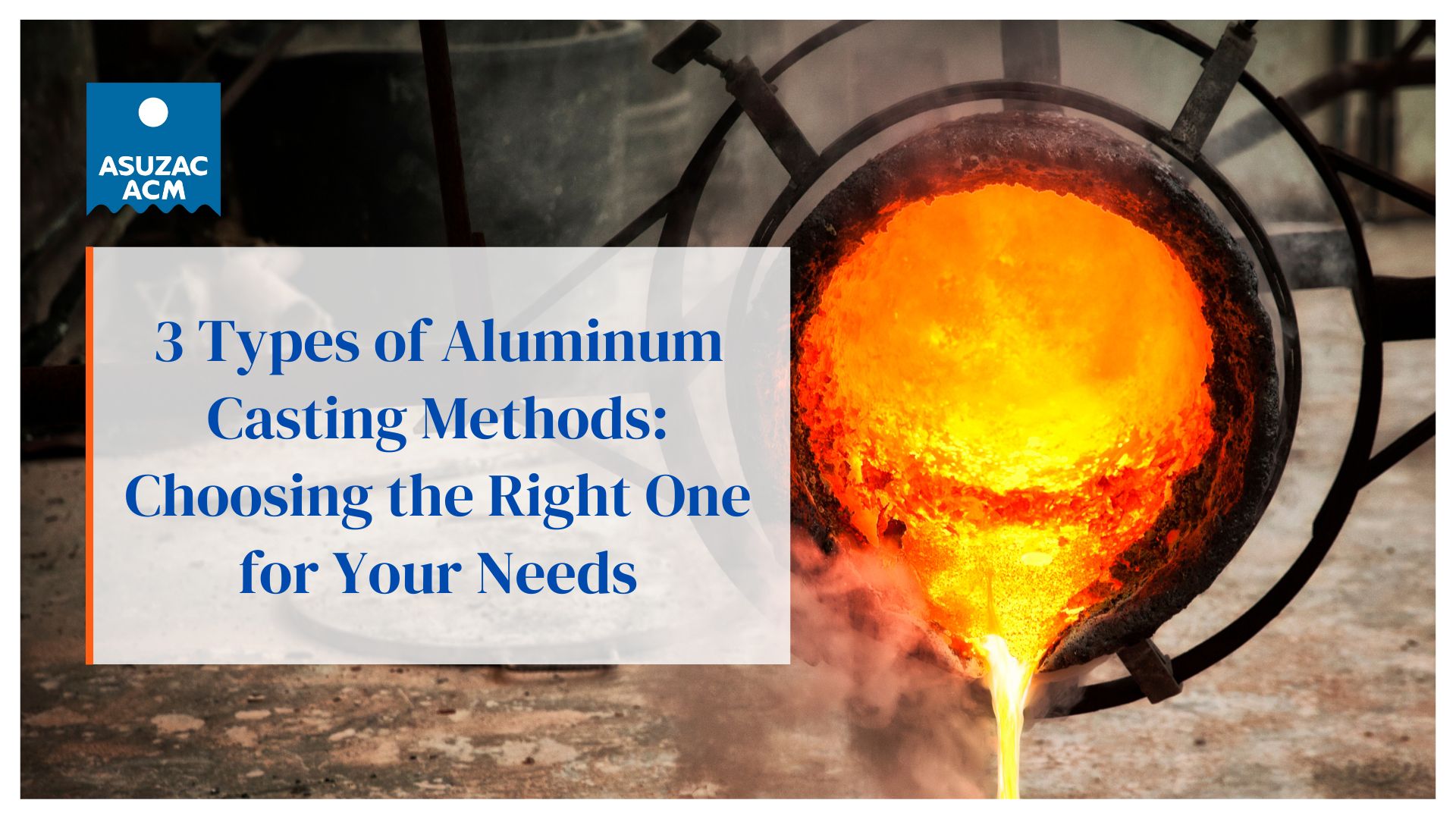
3 Types of Aluminum Casting Methods: Choosing the Right One for Your Needs
Comments
0 Likes
Need Assistance?
Contact our team today for prompt support or inquiries about our products and services!
No 1A. Street No.8, Vietnam-Singapore Industrial Park, Thuan An City, Binh Duong Province, Vietnam.
Monday-Friday: 9am to 5pm; Satuday: 10ap to 2pm
Table of Contents
Aluminum casting is a crucial manufacturing technique used to create strong, lightweight, and complex components for industries like automotive, aerospace, and electronics. Depending on the required precision, volume, and durability, different casting methods are employed to achieve optimal results. Understanding these methods can help businesses make informed decisions when selecting the most suitable aluminum casting process.
In this article, we’ll explore three primary aluminum casting techniques, highlighting their benefits, applications, and how they compare in terms of cost-effectiveness, precision, and scalability.
Sand casting is a traditional and widely used process where molten aluminum is poured into a sand-based mold. Once the metal solidifies, the mold is broken to reveal the cast part. This technique is valued for its simplicity and ability to produce a wide range of component sizes and complexities.
Key Benefits:
Common Applications:
Permanent mold casting uses reusable metal molds instead of sand, allowing for more consistent and precise castings. The molten aluminum is poured into the mold, and once cooled, the part is removed without destroying the mold. This process offers improved mechanical properties due to better control over cooling rates.
Key Benefits:
Common Applications:
Die casting is an advanced process where molten aluminum is injected into a steel mold under high pressure. This technique allows for rapid production and highly detailed components with tight tolerances, making it ideal for industries requiring mass production.
Key Benefits:
Common Applications:
As a leading aluminum casting manufacturer from Japan, ASUZAC ACM stands out for its commitment to innovation, quality, and efficiency. We offer top-tier aluminum casting services tailored to various industrial applications.
Advanced Technology & Innovation
Our patented V-Process revolutionizes aluminum casting, ensuring premium quality and precision. This innovative method enhances the mechanical properties of cast aluminum, providing greater strength and durability.
In-House Production Control
We manage every stage of production, from design to final casting, maintaining strict quality standards. Our integrated approach allows for faster turnaround times and reduced manufacturing defects.
Customer-Centric Excellence
We prioritize customer needs, adapting our expertise to deliver reliable, high-performance aluminum cast products. Whether you require small-batch custom castings or large-scale production, we provide tailored solutions to meet your specifications.
Choosing the best aluminum casting method depends on factors like production volume, surface finish, cost-effectiveness, and mechanical properties. Each technique offers distinct advantages, making it essential to assess your specific project requirements before selecting a casting process. Regardless of your needs, ASUZAC ACM is here to provide top-quality aluminum casting solutions with cutting-edge technology and expert craftsmanship. Contact us today to discuss your aluminum casting needs and discover how we can support your manufacturing goals.