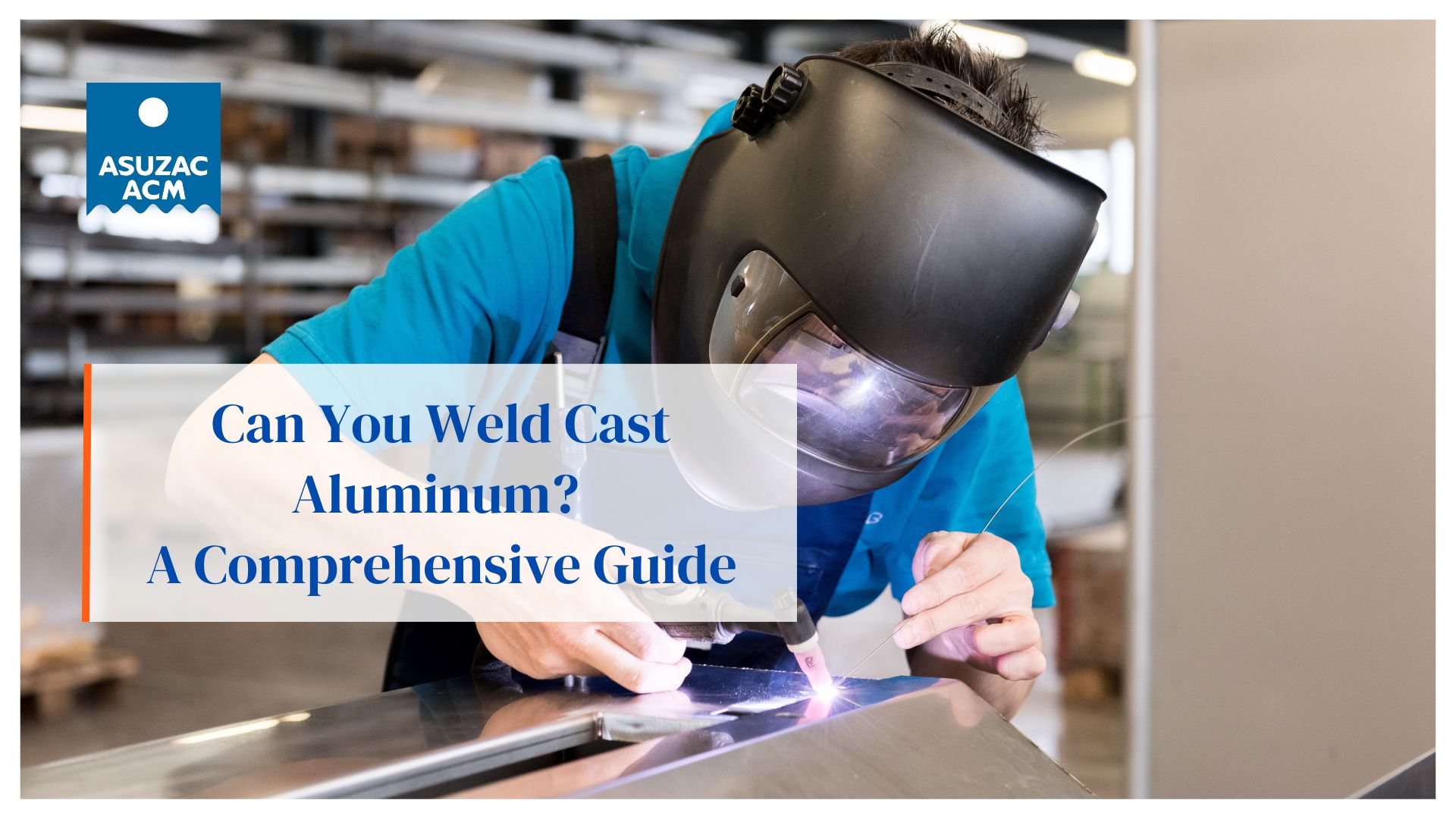
Can You Weld Cast Aluminum? A Comprehensive Guide 2025
When it comes to working with cast aluminum, one question often arises: Can you weld cast aluminum? The short answer is yes, but the reality is far more nuanced. Weldability depends on several critical factors, including the alloy composition and the casting process used. Whether you’re a hobbyist repairing a cracked aluminum part or a professional in an industrial setting, understanding these elements is key to achieving strong, reliable welds. In this article, we’ll dive deep into the world of cast aluminum welding, explore the challenges and solutions, and introduce ASUZAC ACM, a leading aluminum casting manufacturer renowned for producing high-quality castings that meet diverse industry needs.
Table of Contents
Understanding Cast Aluminum and Its Weldability
Cast aluminum is widely used across industries like automotive, aerospace, and manufacturing due to its lightweight nature, corrosion resistance, and versatility. Unlike wrought aluminum, which is shaped through rolling or extrusion, cast aluminum is formed by pouring molten metal into molds. This process creates unique properties that influence how well it can be welded.
The weldability of cast aluminum hinges on two primary factors:
- Chemical Composition: The alloy’s makeup determines whether it can withstand the heat of welding without cracking or forming defects.
- Casting Method: The way the aluminum is cast—whether through sand casting, permanent mold casting, or die casting—affects its internal structure and gas content, which can impact welding outcomes.
Let’s break these down further to understand when and how you can successfully weld cast aluminum.
Read More: 3 Types of Aluminum Casting Methods: Choosing the Right One for Your Needs
Â
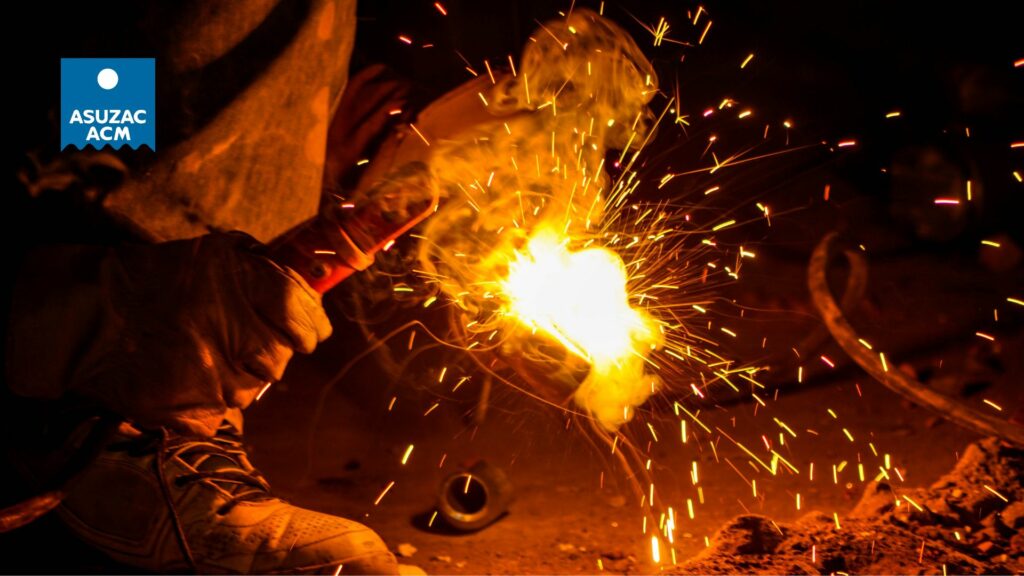
Aluminum Alloy Families and Their Weldability
Aluminum casting alloys are grouped into families based on their chemical composition, each with distinct weldability characteristics. Here’s a closer look:
- 1XX Alloys (Pure Aluminum): These are nearly pure aluminum alloys, often used for their excellent corrosion resistance and electrical conductivity. They’re highly weldable, and a 1100 filler metal is typically recommended.
- 2XX Alloys (Aluminum-Copper): Similar to wrought 2024 alloys, these are strong but tricky to weld due to their susceptibility to cracking. In most cases, welding is not advised unless you’re working with specific exceptions like 2319 filler.
- 3XX Alloys (Aluminum-Silicon-Magnesium): Representing 80-90% of cast aluminum parts (e.g., 356, 357, 319), these alloys are the most common and highly weldable. A 4043 filler metal is the go-to choice for strong, crack-free welds.
- 5XX Alloys (Aluminum-Magnesium): These non-heat-treatable alloys, such as 535, are also easy to weld, especially with a 5356 filler. They’re often found in marine and structural applications.
- 7XX Alloys (Aluminum-Zinc-Magnesium): Comparable to 7075 wrought alloys, these are high-strength but prone to cracking during welding, making them generally unsuitable for the process.
If you’re unsure of the alloy type, the odds are in your favor with 3XX alloys, given their prevalence. In such cases, starting with a 4043 filler is a safe bet, as it works well for the majority of castings you’re likely to encounter.
The Role of Casting Methods in Weldability
The method used to create a cast aluminum part plays a significant role in its weldability. Here’s how the three most common processes stack up:
- Sand Casting: Molten aluminum is poured into a sand mold, which cools slowly due to the mold’s low thermal conductivity. This slow cooling allows gases to escape, resulting in low porosity and excellent weldability.
- Permanent Mold Casting: Similar to sand casting, this method uses reusable metal molds, offering a balance of quality and efficiency. The gradual cooling process keeps gas content low, making these castings easy to weld.
- Die Casting: Designed for high-speed production, die casting injects molten aluminum into a water-cooled steel mold, causing rapid solidification. This traps gases, creating porosity pockets that can disrupt welding. While die castings can be welded, they often require extra care to address sputtering or blowouts caused by gas pockets.
To identify a die casting, look for a smooth surface, thin walls (typically 1/8 to 3/16 inches), and ejector pin marks—small circular impressions left by the mold’s removal mechanism. If you spot these, expect potential challenges and plan for additional weld repairs if porosity arises.
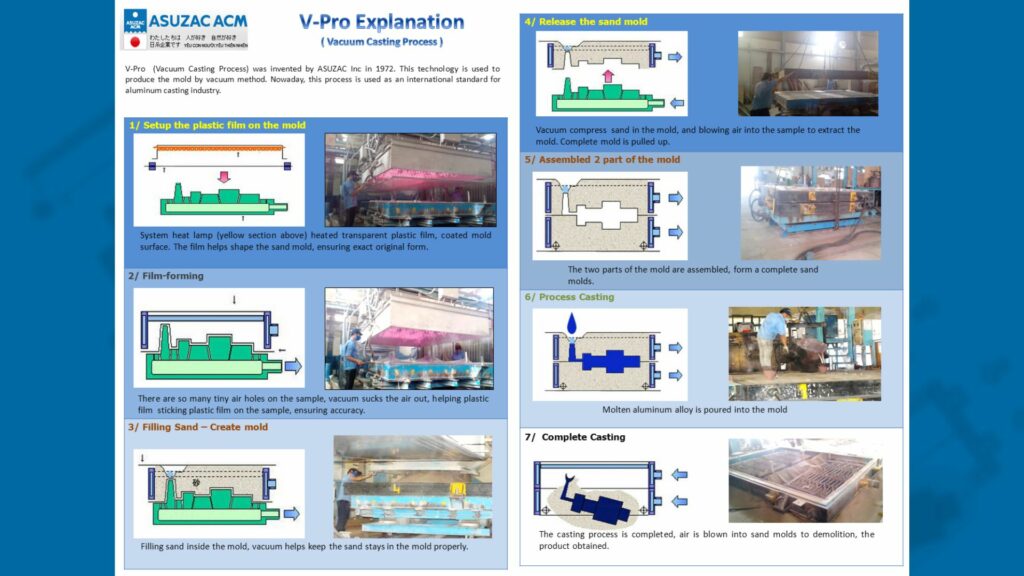
ASUZAC ACM: Pioneering Aluminum Casting with V-Process Technology
For top-quality cast aluminum that’s optimized for welding, ASUZAC ACM stands out as an industry leader. Based in Japan, this innovative manufacturer serves industries like automotive, electronics, and aerospace with precision-engineered castings. What sets ASUZAC ACM apart is its proprietary V-Process Technology, a vacuum-assisted molding technique that revolutionizes aluminum casting.
The V-Process, or vacuum molding, uses a thin plastic film and vacuum pressure to shape sand molds with exceptional precision. This results in castings with smooth surfaces, tight tolerances, and significantly reduced porosity compared to traditional methods. For welders, this means fewer gas-related defects and a cleaner, stronger weld. ASUZAC ACM’s mastery of this technology ensures their castings are not only high-performing but also ideally suited for welding applications. Learn more about their cutting-edge solutions at asuzac-acm.com.
How to Weld Cast Aluminum: Practical Tips
Ready to weld your cast aluminum piece? Here’s a step-by-step guide to ensure success:
- Identify the Alloy (If Possible): If you know the alloy, choose the appropriate filler (e.g., 4043 for 3XX, 5356 for 5XX). If not, default to 4043 as a versatile option.
- Clean Thoroughly: Remove dirt, oil, and oxides using a degreaser like acetone and a stainless steel brush. Contaminants can weaken the weld.
- Assess the Casting Type: Check for signs of die casting (smoothness, thinness, ejector marks). If present, be prepared for porosity issues.
- Preheat (Optional): For thicker parts or die castings, preheating to 200-300°F can reduce thermal shock and improve weld penetration.
- Weld with Care: Use TIG (GTAW) or MIG (GMAW) welding, adjusting settings for aluminum’s high thermal conductivity. Watch for gas pockets in die castings—grind and reweld if necessary.
- Inspect and Finish: After cooling, check for cracks or porosity. Multiple repair cycles may be needed for die castings.
Challenges and Solutions in Welding Cast Aluminum
Welding cast aluminum isn’t without its hurdles. Porosity, cracking, and filler mismatch are common issues, but they’re manageable with the right approach:
- Porosity: Prevalent in die castings, this can cause weld blowouts. Grind out affected areas and reweld until clean.
- Cracking: Avoid 2XX and 7XX alloys if possible, as their chemistry promotes cracking. Stick to 3XX or 5XX for better results.
- Unknown Alloy: When in doubt, 4043 filler is a reliable starting point, effective for most scenarios.
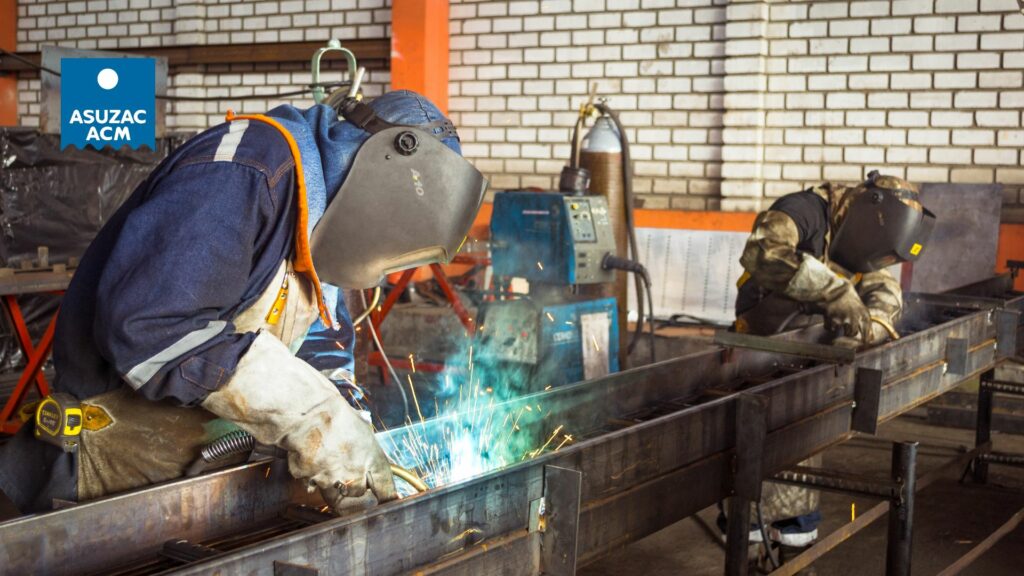
Why Choose Cast Aluminum for Welding Projects?
Cast aluminum’s appeal lies in its adaptability. It’s lightweight yet durable, making it a favorite for everything from engine blocks to decorative pieces. When sourced from top manufacturers like ASUZAC ACM, you’re starting with a product designed for performance, reducing welding headaches and ensuring long-lasting results.
Â
Conclusion: Yes, You Can Weld Cast Aluminum—With the Right Knowledge
So, can you weld cast aluminum? Absolutely, provided you understand the alloy and casting method you’re dealing with. Most castings, especially 3XX and 5XX alloys from sand or permanent mold processes, are straightforward to weld with the right filler and technique. Even die castings, though trickier, are manageable with patience and preparation.
For the best outcomes, partner with a trusted supplier like ASUZAC ACM, whose expertly crafted castings set the stage for welding success. Whether you’re tackling a repair or a custom fabrication, this guide equips you with the insights to weld cast aluminum confidently. Ready to get started? Grab your torch, choose your filler, and let the sparks fly!