
Die Casting vs Vacuum Casting: A Comprehensive Comparison
Aluminum casting is a versatile manufacturing process that creates precise, durable components for industries like automotive, architecture, and consumer electronics. Among the various techniques, die casting and vacuum casting are two prominent methods, each offering unique advantages suited to specific applications. While both processes produce high-quality parts, their approaches, materials, and outcomes differ significantly, making it essential to understand their distinctions to choose the right method for your project.
In this article, we dive into a detailed comparison of die casting and vacuum casting, exploring their processes, benefits, and limitations. We also introduce ASUZAC ACM, a leading aluminum casting manufacturer renowned for our innovative V-Process Technology and our ability to deliver exceptional cast products globally.
Table of Contents
Understanding Die Casting and Vacuum Casting
Die Casting involves injecting molten metal, typically non-ferrous alloys like aluminum, zinc, or magnesium, into a reusable steel mold (called a die) under high pressure. The metal quickly cools and solidifies within the mold, forming a precise, solid part that is then ejected. This method is known for its speed and accuracy, making it ideal for high-volume production.
Vacuum Casting, often called silicone molding or polyurethane casting, uses a silicone mold created from a master pattern. A liquid resin, typically polyurethane or similar plastics, is poured into the mold under vacuum pressure to eliminate air bubbles, ensuring a detailed, high-quality part. This method excels in prototyping and low-volume production.
ASUZAC ACM: Your Leader in Aluminum Casting
At ASUZAC ACM, a Vietnam-based subsidiary of the ASUZAC Group, we pride ourselves on being a premier aluminum casting manufacturer celebrated for our cutting-edge V-Process Technology. Our vacuum-assisted casting method uses plastic film and vacuum pressure to create flawless sand molds, producing parts with smooth surfaces, intricate details, and exceptional durability. We specialize in a wide range of products, including facades, bollards, mailboxes, and outdoor furniture, serving industries such as construction, architecture, and urban planning.
Our notable projects include supplying aluminum castings for iconic building facades, durable garden lighting bollards, and custom mailboxes for apartment complexes worldwide. With a commitment to quality and sustainability, we deliver globally, ensuring precision and reliability in every project. For inquiries or custom orders, visit our contact page.
Comparing Die Casting and Vacuum Casting
To help you choose the right method, we’ve outlined a comparison of die casting and vacuum casting across key factors:
Aspect | Die Casting | Vacuum Casting |
Process | Molten metal is injected under high pressure into a steel mold, solidifying into a part. | Liquid resin is poured into a silicone mold under vacuum to remove air bubbles. |
Materials | Non-ferrous metals (aluminum, zinc, magnesium alloys). | Plastics (polyurethane resins, silicone rubber, low-temperature curing plastics). |
Complexity | Produces complex metal parts with high precision and thin walls. | Replicates intricate details and complex geometries, ideal for prototypes. |
Production Volume | High-volume production with fast cycle times and consistent quality. | Low-volume production and prototyping, cost-effective for small batches. |
Strength & Durability | High mechanical strength, ideal for strong, lightweight parts. | Good mechanical properties, but less durable than metal castings. |
Surface Finish | Smooth, high-quality finish due to metal molds and high-pressure injection. | High-quality finish, dependent on mold quality and post-processing. |
Cost | High initial mold costs, but cost per part decreases with volume. | Lower mold costs, cost-effective for small-scale production and prototyping. |
Tooling | Requires specialized steel molds, increasing lead times and modification costs. | Uses silicone molds, easier and cheaper to produce and modify. |
Applications | Automotive, aerospace, electronics (e.g., engine parts, housings, brackets). | Product design, prototyping, medical devices, architectural models. |
Tolerance Range | ±0.05 mm to ±0.2 mm (±0.002″ to ±0.008″). | ±0.1 mm to ±0.3 mm (±0.004″ to ±0.012″). |
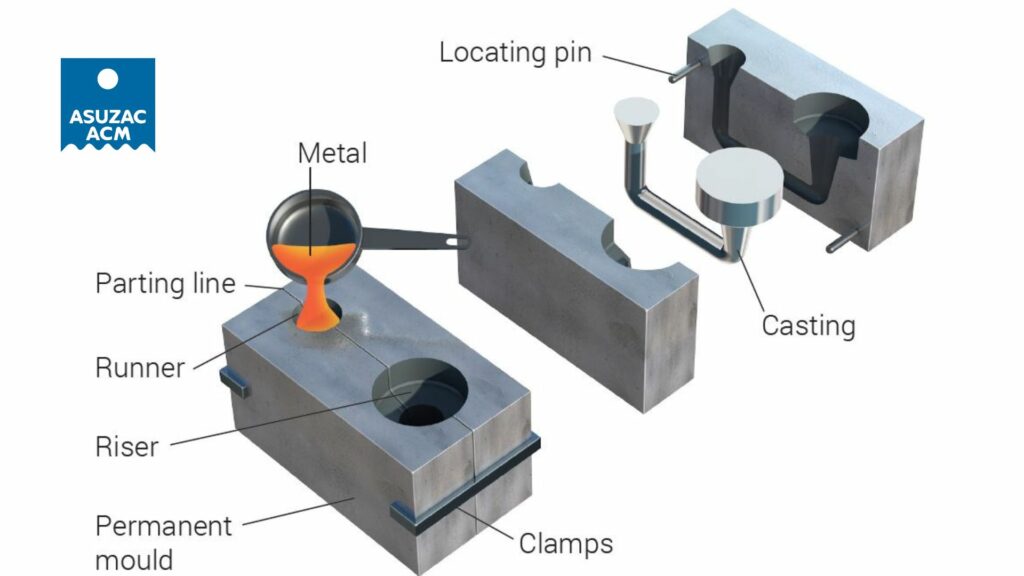
Advantages of Die Casting
Die casting offers several benefits, particularly for aluminum casting:
- Precision Craftsmanship: Creates complex shapes with tight tolerances and thin walls, perfect for intricate designs.
- High Efficiency: Rapid cycle times and minimal material waste make it cost-effective for large-scale production.
- Consistent Quality: Ensures uniform parts with excellent mechanical properties and dimensional stability.
- Robust Strength: Produces strong, lightweight parts ideal for demanding applications like automotive components.
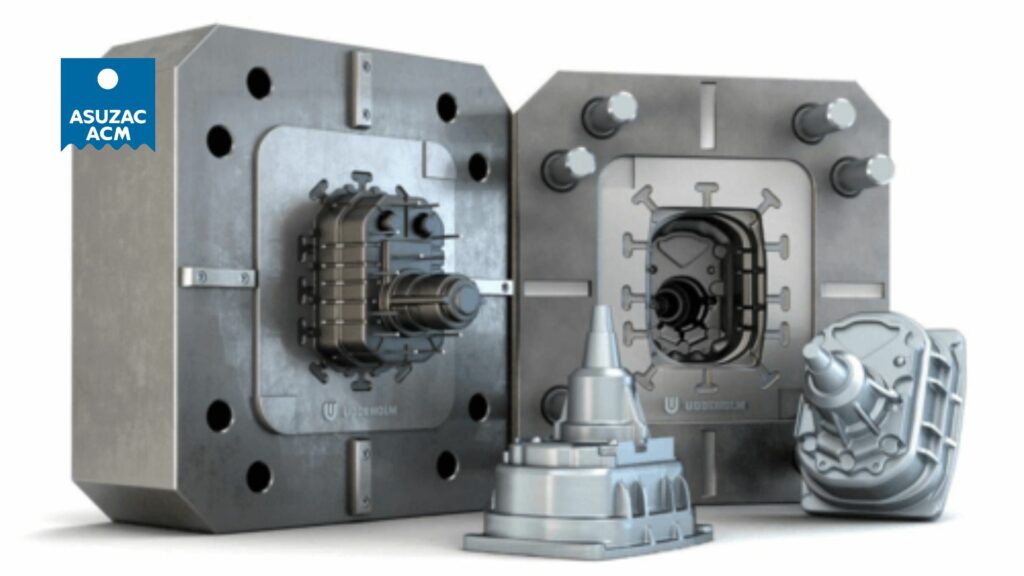
Advantages of Vacuum Casting
Vacuum casting is ideal for specific use cases, especially prototyping:
- Superior Surface Detail: Delivers smooth surfaces and fine textures, perfect for aesthetically driven parts.
- Material Flexibility: Supports a variety of plastics, including resins and elastomers, for diverse applications.
- Cost-Effective for Small Runs: Affordable silicone molds make it suitable for prototypes and small batches.
- Complex Geometries: Accurately reproduces intricate features, ideal for detailed models or medical devices.
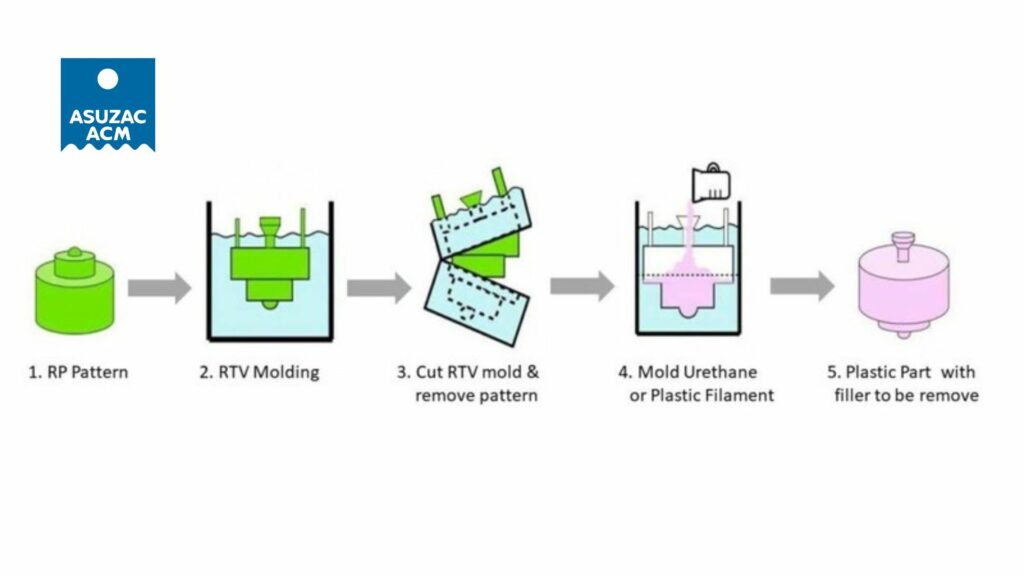
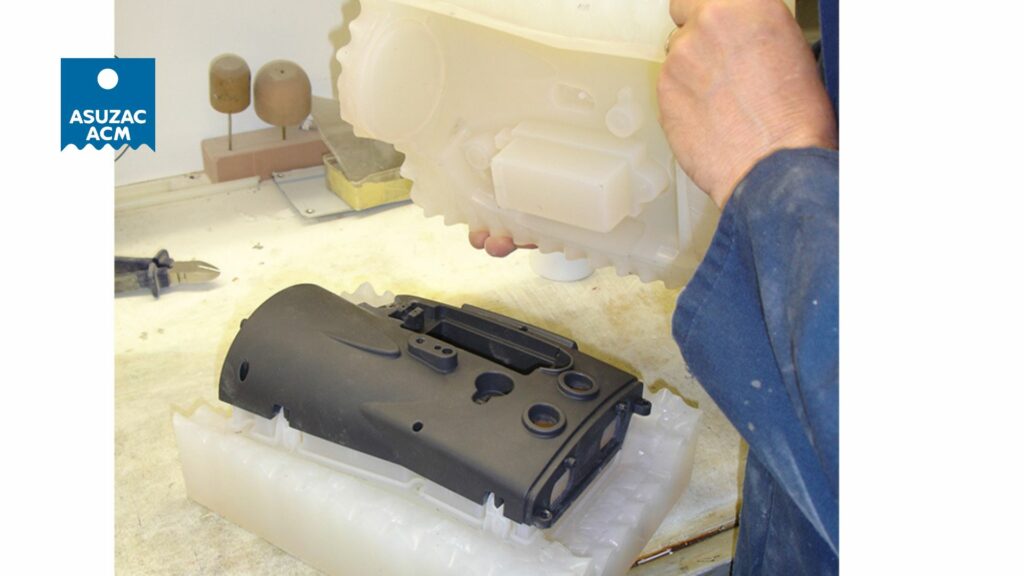
Â
Limitations to Consider
- Die Casting: High tooling costs and longer lead times for mold production make it less ideal for small runs. Modifying steel molds can be costly.
- Vacuum Casting: Parts may lack the strength of metal castings, and surface finish depends on mold quality and post-processing. It’s less efficient for high-volume production.
Choosing Between Die Casting and Vacuum Casting
- Opt for Die Casting for high-volume production of strong, precise metal parts, such as aluminum components for automotive or electronics industries.
- Choose Vacuum Casting for prototyping, small-batch production, or parts requiring high surface detail, like plastic models or medical devices.
Our V-Process at ASUZAC ACM enhances die casting by offering a hybrid approach, delivering aluminum parts with the precision of die casting and the flexibility of vacuum-based molding, perfect for custom projects like architectural facades or bollards.
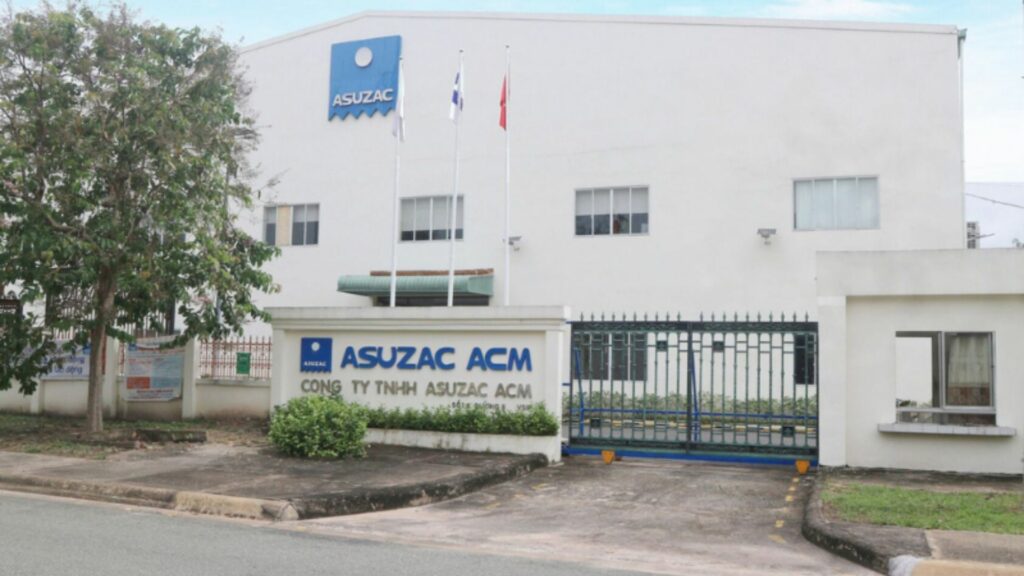
FAQ: Die Casting and Vacuum Casting
Q: What is the difference between die casting and mold casting?
A: Die casting injects molten metal into steel molds under high pressure, producing highly accurate parts with thin walls and smooth surfaces. Permanent mold casting is slower, using reusable molds with less precision but more affordable tooling.
Q: What are the two types of die casting machines?
A: Die casting machines include hot-chamber (used for low-melting-point metals like zinc) and cold-chamber (for higher-melting-point metals like aluminum), rated by clamping force.
Q: What is the difference between a mold and a die?
A: A mold shapes materials by allowing them to solidify, often for plastics or molten metals, while a die cuts or forms materials, typically metals, using mechanical force.
Q: What is the die casting process?
A: Die casting involves rapidly injecting molten non-ferrous alloys (e.g., aluminum, zinc, magnesium) into steel dies under high pressure to create precise, molded parts.
Q: What is the V-Process of ASUZAC ACM?
A: Our V-Process is a vacuum-assisted casting method that uses plastic film and vacuum pressure to form precise sand molds. It produces aluminum parts with smooth finishes, intricate details, and minimal defects, ideal for facades, bollards, and mailboxes. Learn more at our V-Process page.
Contact ASUZAC ACM for Your Casting Needs
Ready to explore aluminum casting for your project? We’re here to assist:
- Phone: +84 274 376 7136 | +84 093 707 6608
- Email: [email protected]
- Website: Contact Us
Conclusion: Partner with ASUZAC ACM for Aluminum Casting Excellence
Die casting and vacuum casting each offer distinct advantages in aluminum casting, with die casting excelling in high-volume metal parts and vacuum casting ideal for prototyping and small-batch plastics. At ASUZAC ACM, we leverage our innovative V-Process to deliver precision-cast aluminum products, from architectural facades to durable outdoor furniture, for projects worldwide. Our commitment to quality and sustainability makes us your ideal partner for casting needs.
Visit top casting aluminum manufacturer to explore our expertise, check out our V-Process technology, or reach out via our contact page to start your project with ASUZAC ACM today.
Â